The COVID-19 pandemic has been a massive disruptor of supply chain operations worldwide, logistics operations worldwide. Every aspect of supply chain planning, including demand planning, supply planning, inventory management, strategic network design, and sales and operations planning (S&OP), has seen its fair share of risk and uncertainty. Companies suffered from sudden surges in raw material prices, delivery delays, demand-driven stresses, and production costs. An EY survey reports that only 2% of the companies were prepared for the disruptions, while 72% faced adverse effects. The pandemic changed the dynamics of supply chain management. Now, the spotlight is on optimized and resilient supply chain planning and forecasting.
Tackling Supply Chain Risk and Uncertainties with Well-forecasted Supply Chain Planning
Let's face it; supply chain performance gaps are real. Most supply chain operations are far from optimal; the distributed nature of a supply chain causes difficulties. This nature can be seen through the multiple locations and organizations covered by a single supply chain, and the flow of materials, information, and finances which happens within them. External factors, like labor strikes, pandemics, conflict, or natural disasters, also contribute to uncertainty and causing vulnerability.
Optimizing uncertain supply chains calls for accurate supply chain forecasts, without which measures such as improved supplier network management are ineffective. Businesses should be able to predict fluctuations in demand, supply, commodity prices, and labor availability, as well as the changing costs of production, labor, logistics, and energy. In other words, supply chain management requires execution of supply chain planning, leveraging accurate forecasting on the variables we call 'outcome' which are interdependent with the 'input', or the uncertain variables. To this end, deterministic forecasting has always been a popular approach on which to base supply chain planning.
What is Deterministic Planning?
A supply chain planning model based on deterministic forecasting assumes that both the outcome and its corresponding input variables have fixed values. For instance, take the case of a chef who has determined the amount of meat, vegetables, oil, and gas for preparing the same menu in the same quantity, for, say, a month. This kind of inventory management is based on the assumption that day-to-day demand will be constant, alongside the procurement cost and the supply. Deterministic forecasting works satisfactorily for situations where the factors are somewhat predictable.
Deterministic demand forecasting can also be applied to supply chain management in a medium-sized retail chain. Many businesses like this found just-in-time supply management to cause delays during the pandemic. Their aim is then to optimize their inventory strategy, for example through minimizing the frequency of material orders, reducing holding costs, and avoiding the losses caused by stock-outs. The variables here include total demand, the days of sales, customer demand per day (and therefore the losses due to stock-outs), lead times for the materials, production cost and more. These variables will usually produce real-time data which can be used to build the model.
The order/delivery costs from the supplier and holding costs are outcomes as they rely on the values of other variables. A deterministic model considers all these variables as constants. For example, it assumes that the customer demands ten units every day, and that the holding cost will remain the same through the year. Each variable is given a determined value, so the outcomes will have a determined value too.
Pros of Deterministic Planning
The deterministic model uses data to build clear pictures of demand, taking variables and generating real-world cases. It does not rely on confusing algorithms and provides end-to-end transparency to supply chain managers. It provides data-driven answers, and, using these answers, companies can (if all goes to plan) see cross-functional benefits. To put it simply, the approach is, well, simple.
Cons of Deterministic Planning
Deterministic planning model lacks one main ability: to acknowledge the uncertainty of a value. Take, for example, the case of the chef or the mid-sized retail outlet whose deterministic planning model does not consider the consequences of certain weather events, of unexpected closures, or of disruptions to production plans. It doesn't consider constraints to supply or sudden demand increases. This is poor supply chain management when applied in, for instance, complex operations in industries such as energy and utilities, chemical, metals and mining, or industrial products and machinery.
Demand planning in these industries increasingly uses the probabilistic approach. This approach uses conditional probability, which is where one event is more or less likely to occur IF another event occurs. Meaning that, if an event can be predicted more accurately, so too can the uncertainty of the prediction made on the demand.
What is Probabilistic Planning?
Probabilistic, or stochastic, planning, does not render deterministic planning obsolete. In fact, even where ERP systems provide accurate data for all values, a deterministic approach can yield satisfactory planning outcomes with little deviations. However, a probabilistic planning model is better at considering uncertainties in the input variables, leveraging historical and statistical data to forecast a range of possible outcomes to support decision making. The model delivers realistic forecasting by being inherently more granular in considering all the factors relevant to supply and demand planning.
With a probabilistic supply chain planning model, our hypothetical chef can better forecast the increase or decrease in demand by considering the occurrences of holidays, lockdowns, or even local events near his restaurant that will raise footfall.
Generally, a probabilistic model considers three scenarios; first, if all occurs as planned for; second, if some small but reasonably likely events occur; and third, black swan style events. Then, a probability distribution of the results is plotted to find the probabilities of each scenario. The stochastic approach works best for value chains where risks are extremely difficult to predict but have huge effects when they occur. This would then be most appropriate to apply in multi-echelon supply chains, or during continuous, long-term disruption caused by the pandemic.
Take the example of a utility or power distributor using the probabilistic approach to forecast demand loads, and therefore optimize energy system management. The input variables considered to predict energy consumption are outlined in the building energy model (BEM), which specifies how home devices are being used. Apart from this, external weather is also considered as an uncertain parameter. This methodology allows the planning team to build their competitive advantage through a point load forecast that considers even weather forecast data.
Pros of Probabilistic Planning
The probabilistic planning model uses impartial statistical rules to reflect real-world scenarios. It lets the planning team predict a range of multiple outcomes, providing a less rough-cut forecast. In addition, this model better acknowledges the variability of supply chain planning inputs, allowing the use of buffer time to deal with delays at any stage of a supply chain.
Cons of Probabilistic Planning
Since the variables are probabilistic, it's often difficult to define the relationships between different variables. The model is always dependent on a 'base mode/case,' which must be configured so that the probability adjustments can be made to the base case. Also, in more complex probabilistic planning models, the link between the statistical realizations and the real-world outcomes becomes less clear. And it almost goes without saying, that probabilistic planning requires an incredible amount of computer power.
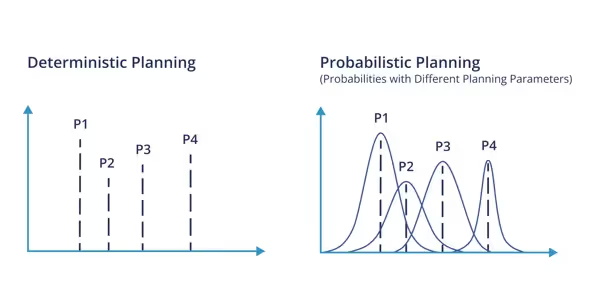
Final Thoughts: Combining the Approaches
The field of supply chain management is undecided on which approach is more effective. While neither methodology is perfect, they each serve different purposes and different levels of uncertainty. Logically, using both approaches could increase the forecasting effectiveness and ultimately generate a probabilistic model with deterministic results. On the other hand, there are more sophisticated multiple models available. the multiple probabilistic and multiple deterministic approaches are both worth learning about, but that is a topic for another day.
Before adopting either, it's recommended to formulate an uncertainty matrix that ranks possible risks based on scale and impact on the outcomes. The deterministic approach would be more viable in scenarios with highly unstable variables, where less data is available. On the other hand, values with sufficient historical data could be used to create probability distribution functions, and attain more realistic outcomes.
It's good for most companies to test a combination of single and multiple probabilistic or deterministic supply chain planning approaches to ensure consistent outcomes. To this end, aioneers' AI-powered solutions for supply chain planning prove to be an ideal tool for organizations across various industries.
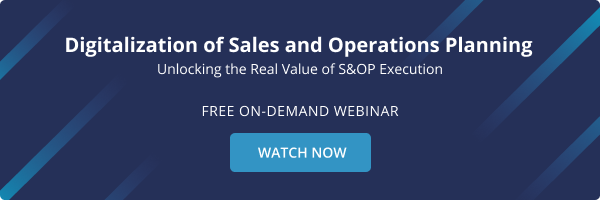